The expenses for research and development in the business year 2011/12 amounted to EUR 116.7 million. Due to ongoing improvements in efficiency, including in the area of R&D organization, actual expenditures remained significantly below the available R&D budget of more than EUR 120 million, while all of the planned projects were consistently implemented.
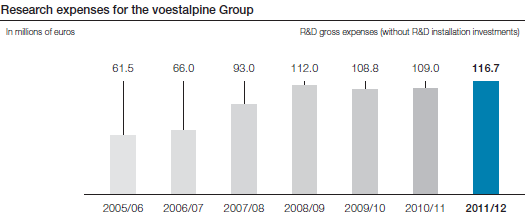
For the current business year 2012/13, the voestalpine Group has a research and development budget of EUR 132.3 million; this corresponds to another increase of the funds being made available for technology and innovation by 9.4%, equaling the highest figure by far in the history of the company. In the long-term analysis, the voestalpine Group raised its R&D expenditures during the past ten years by an average of 11% per year.
The research ratio of the Group (share of R&D expenses of total sales) at the end of the business year 2011/12 was 1.0% (previous year: 1.0%), the R&D coefficient (R&D expenditures measured by economic value added) was 2.61% (previous year: 2.55%).
Conforming to the Group’s strategic direction, the focus of research and development is on the most sophisticated product and materials solutions for applications in the mobility and energy sectors. The top priority is the development of innovative complete solutions that guarantee optimum customer benefit while reducing life cycle costs.
One of the main strengths of the Group is the combination of all the necessary competencies and steps that create added value; for example, materials development is typically accompanied by the development of processing technologies (such as forming or joining processes), tool steel grades, and welding filler materials.
Current research and development highlights
One of the most significant innovations that has resulted from our R&D work is without a doubt the phs®-ultraform technology, which was presented to the broad professional community for the first time at the Geneva Motor Show in the spring of 2012. The acronym “phs” stands for “press hardening steel.” It is used primarily for safety-relevant automobile components that are lightweight but also extremely high-strength (up to 1,800 megapascal), offering cathodic corrosion protection and providing the possibility of processing blanks with various combinations of strength and thicknesses (“tailored property parts”). Thus, phs-ultraform is making a significant contribution to lightweight automobile construction, which means that it is ideally suited for applications in electric mobility. After the already very successful market launch of the “indirect” manufacturing process, in the business year 2011/12, another significant breakthrough was made that now enables the production of these components by way of the “direct process.”
The zinc-magnesium coating of steel strip and sections, which has already been successfully adopted in the construction sector, is making an outstanding contribution to the preservation of resources: by adding magnesium through alloying, the corrosion resistance of zinc surfaces is substantially improved, enabling a reduction of the thickness of the coating while retaining the same protective effect. Currently, this coating technology is being developed further for use in the automobile sector.
High-speed rails, which were newly developed on the basis of the special microstructure bainite, are currently in the intensive and lengthy phase of track and certification tests. Initial results thus far have shown zero defect operation as anticipated compared to the reference rails made of pearlite.
The voestalpine VAE Group, global market leader in turnout technology and last year’s recipient of the “Best Service Provider of the Rail Industry” prize, received another international award in February 2012: the company received the highly respected “Middle East Rail Award” in the category “Most Innovative Use of Technology” for the development of a hot box and brake detection system that is particularly geared to desert climate conditions.
The goal of the ongoing Group project “Power plant 50plus,” another important R&D endeavor, is the improvement of the efficiency of thermal power plants. By using new and/or improved materials for power plant components, it is already possible to increase the efficiency of steam power plants from 42% to 52%. As is the case for the previously described mobility innovations, these developments are also largely technologically unique, cutting-edge developments, with the voestalpine Group the only company worldwide that is providing them in this form.
In the sector of renewable energies, the photovoltaic system for flat roofs developed by voestalpine Polynorm B.V. deserves mention. It was successfully launched on the market under the brand name “iFIX.” The system has an optimum structural shape, and its particular advantage is minimal assembly effort at the construction site.
The Profilform Division has met the demand for weatherproof tube cross-sections to be used as supports for photovoltaic installations by developing a cross-section made of coil-coated steel strip that has been optimized with regard to corrosion resistance; a patent has been filed. With the development and market launch of a system for mounting cross-sections without needing tools by Metsec plc (Great Britain), competitiveness has been considerably improved by reducing assembly effort.
The continued optimization of resource use in production continues to have a high priority in the Group’s R&D activities. For example, a method was developed in the special steel plant in Hagfors (Sweden) to replace the alloy ferromolybdenum by less expensive additives, achieving the same effect but enabling a significantly higher yield.
Regarding the highlights of our global research and development collaborations with science partners, we refer to the presentations in previous letters to shareholders for the business year 2011/12.